Case Study: Synthesis of an Active Pharmaceutical Ingredient in Water
Introduction
Water is often recognized as a sustainable solvent due to its widespread availability, low cost, safety profile, and low environmental impact. However, many organic reaction components are poorly soluble in water. In these cases, use of surfactant like TPGS-750-M (Figure 1) can often improve aqueous solubility, enabling chemistry in water. Recent work in this area has demonstrated that a wide variety of chemical transformations can be adapted to surfactant/water media, presenting an opportunity to replace reaction solvents with water across multi-step synthetic sequences. However, in chemical manufacturing processes, large amounts of solvent are used not only in reactions, but also to purify and isolate products. To realize the full environmental benefits of conducting chemistry in water, it is therefore important to find ways to avoid solvent use during the work-up and purification of products synthesized in water.
Figure 1: Structure of surfactant TPGS-750-M
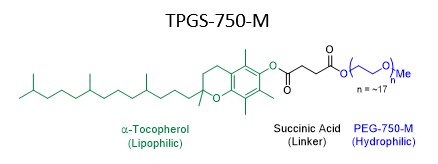
Process chemists and engineers at Takeda Pharmaceuticals did just this, developing a second-generation process to manufacture TAK-954 active pharmaceutical ingredient (API) that is conducted almost entirely in water, including multiple controlled isolations. Compared to the first-generation solvent-based process, the second-generation process in water uses 77% less material inputs, 94% less organic solvent, and 48% less water, while improving overall yield from 35% to 56%.[1]
In this case study, some of the strategies employed by the Takeda team to develop a water-based synthetic process are explained.
Learning Objectives
By the end of this topic you should:
- Understand strategies for designing a synthetic route in water
- Understand how to optimize a reaction in water
- Understand strategies for designing crystallizations from aqueous media
The Starting Point: First-Generation Solvent-Based Process for Production of TAK-954 API
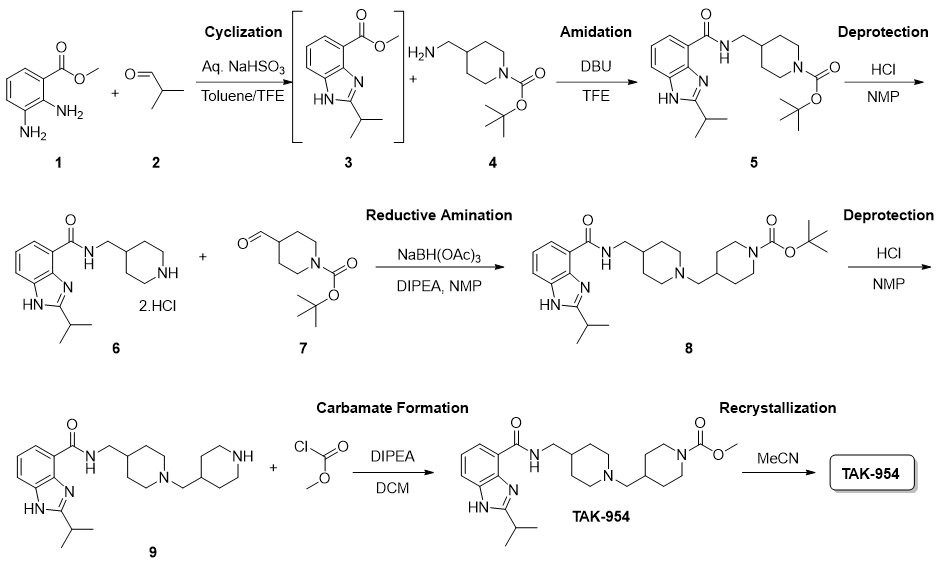
The first-generation TAK-954 process consists of 6 synthetic steps and 6 isolations along with a final recrystallization step to control purity and crystal form of the API. Five separate organic solvents are used across the process. The overall yield is 35%, and the cumulative PMI across the 6-step sequence is 350 kg inputs/kg API.
The End Point: Second-Generation Water-Based Process for Production of TAK-954 API
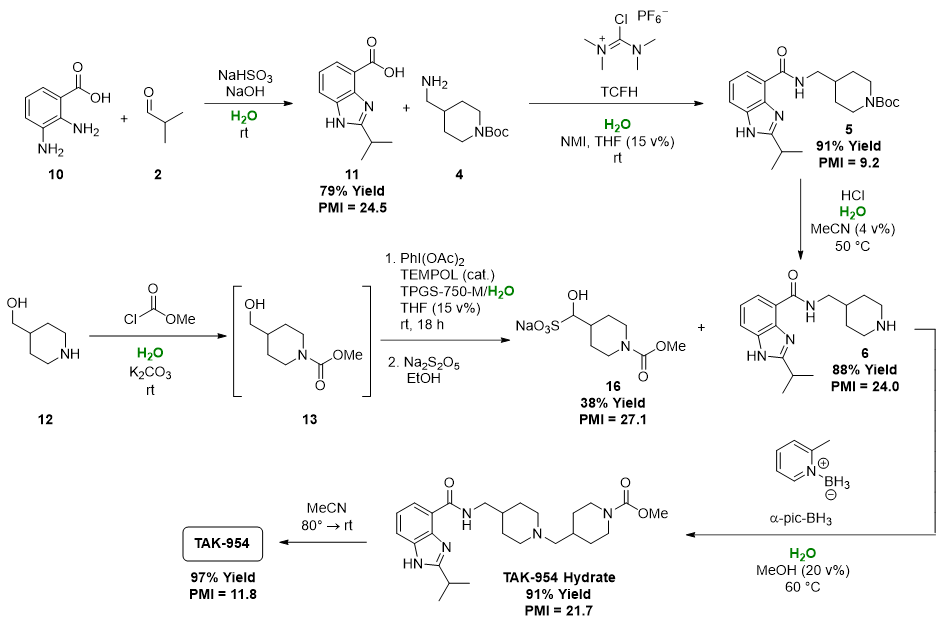
Strategies to Design a Synthetic Route in Water
- Maximize route efficiency. Whether planning a synthetic route in water or using conventional organic solvents, strive to develop the most efficient synthetic route possible by minimizing steps and maximizing convergence.
How it was applied to TAK-954: The first-generation route to TAK-954 features an inefficient protection/deprotection strategy. The second piperidine ring is brought in with compound 7 with its Boc protecting group. This is then immediately removed and replaced with the desired methyl carbamate group. This inefficient protection/deprotection strategy was removed from the second-generation route by introducing the second piperidine ring of compound 16 with the desired methyl carbamate moiety already in place. Piperidine fragment 16 was not commercially available and was therefore synthesized from hydroxymethylpiperidine 12. Because the aldehyde form of 16 is an oil that is difficult to isolate and handle, 16 was isolated as a stable, crystalline bisulfite adduct. - Choose water-compatible chemistry for each transformation. There are often multiple reactions and conditions available to achieve a given chemical transformation. Thoughtfully select chemistry that is compatible with aqueous conditions.
How it was applied to TAK-954: In the first-generation route, direct amidation of methyl ester 11 under basic conditions was used to install piperidine fragment 4. However, under aqueous conditions, this amidation failed to reach full conversion due to competitive hydrolysis of the methyl ester. Instead, this chemistry was replaced with a conventional amide bond formation mediated by a coupling reagent in the second-generation process. This change necessitated using the carboxylic acid analog (10) of starting material 1. - Do not rule out seemingly water sensitive chemistry without trying it. Chemists are trained to go to great lengths to exclude water from reactions. However, even highly reactive chemistries often work under aqueous conditions, either because the desired reaction outcompetes the hydrolysis pathway, or, if micellar conditions are used, reactive species are shielded from surrounding water in the lipophilic interior of the micelles.
How it was applied to TAK-954: Methyl chloroformate is used to install the methyl carbamate moiety of intermediate 13 in the second-generation route. It would be easy to assume that this kind of acid chloride chemistry would be incompatible with water. However, the reaction proceeds cleanly and rapidly in water with nearly quantitative yield.
Optimization of Aqueous Reaction Conditions
- Select water-compatible reagents. Typically, there are many different reagents available to achieve a given chemical transformation. Some reagents may not be water stable, while others might offer superior performance under aqueous conditions. Before screening reagents, consider which might be amenable to aqueous or micellar conditions. The Reagent Guides from the ACS GCI Pharmaceutical Roundtable provide a good starting point for considering the options: https://reagents.acsgcipr.org/
How it was applied to TAK-954: In developing the second-generation process, a variety of amide coupling reagents were screened to achieve the coupling of acid 11 and amine 4. Some reagents performed better than others under aqueous conditions, as seen in the below table (reproduced from [1]).
Table 1 Activating agent screen for amide coupling of intermediates 11 and 4a

Entry | Activating Agent | Base | Conversion to 5 (%)b |
1c | Thionyl Chloride | K₂CO₃ | 59 |
2 | Isobutyl Chloroformate | NMM | 30 |
3 | Cyanuric Chloride | NMM | 19 |
4 | EDCI/HOBt | NMM | 34 |
5 | TNTU | DIPEA | 16 |
6 | EEDQ | None | 22 |
7 | COMU | 2,6-lutidine | 47 |
8 | DMTMM | NMM | 97 |
9 | TCFH | NMI | >98 |
a Reaction conditions: 1.2 mmol 11, 1.2 mmol 4, 2.5 mL TPGS-750-M (2 wt. % in H2O). b HPLC area %. c The acid chloride of 11 was pre-formed in neat thionyl chloride before addition to an aqueous solution of 4 and K2CO3.
- Although the same reductive amination chemistry was used in the first-generation and second-generation routes to install piperidine fragment 7/16, the sodium triacetoxyborohydride reducing agent used in the first-generation route is unstable in water, requiring a large excess and repeated charges of the reducing agent to reach full conversion under aqueous conditions. Instead, α-picoline borane, a water-stable reducing agent known to reduce imines, was selected as reducing agent in the second-generation route.
- Run a control experiment without surfactant. In many cases, the use of a micelle-forming surfactant enables chemistry in water that would otherwise not proceed. However, in some cases the use of a surfactant is unnecessary. Run a control experiment in neat water or water/co-solvent without surfactant to ensure that the surfactant is necessary and beneficial.
How it was applied to TAK-954: Surfactant was found to be unnecessary in the first three steps of the second-generation process. Instead, the chemistry proceeded in water or water/co-solvent mixtures without surfactant. In the case of the amide coupling of acid 11 and amine 4, the presence of surfactant was found to inhibit a reactive crystallization leading to product gumming while offering no advantages in reactivity or conversion. - If micellar conditions are used, screen lipophilic reagents. When a micelle-forming surfactant is used, the goal is for the reaction to occur within the lipophilic interior of the micelles (Figure 2). High effective concentrations of reaction components within the micelles can lead to improved reaction rate, conversion, and selectivity while reducing required reaction temperature and shielding reactive intermediates from the surrounding water. Somewhat counterintuitively, lipophilic reagents can improve reaction performance in micellar water as they tend to migrate to the micelle interiors, increasing the likelihood of reaction within micelles rather than in the surrounding water.
How it was applied to TAK-954: Initially, bleach was screened as terminal oxidant in the TEMPOL-catalyzed oxidation of primary alcohol 13 to aldehyde 16 in the second-generation process. However, significant over-oxidation to the carboxylic acid was observed. The over-oxidation was assumed to result from hydration of the aldehyde product followed by a second oxidation. Aldehyde hydration is more likely to occur in the bulk water rather than within the lipophilic interior of the micelles. To reduce over-oxidation, water-soluble bleach was replaced with phenyliodide diacetate as terminal oxidant. Due to its increased lipophilicity, phenyliodide diacetate will tend to be sequestered within the interior of the micelles, reducing the likelihood that the hydrated aldehyde product, presumed to be located primarily in the bulk water phase, will encounter the oxidant. With this change in terminal oxidant, the over-oxidation byproduct was no longer observed.
Figure 2: Cartoon cutaway view of a micelle, showing the lipophilic interior (yellow) and hydrophilic exterior (white).
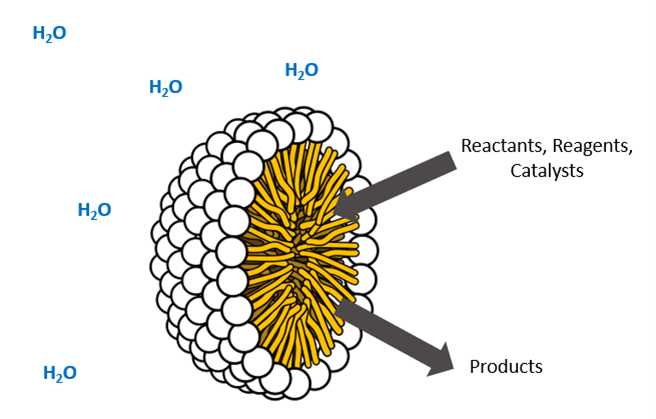
- In addition to standard reaction parameters, screen water-specific parameters such as surfactant identity and amount, co-solvent identity and amount, and pH. When aqueous micellar conditions are used, standard reaction parameters such as time, temperature, stoichiometry, addition rate, etc. should be optimized. However, micellar conditions present additional parameters for optimization. The identity of the surfactant can have a dramatic effect on reaction performance, so multiple surfactants should be screened. Less commonly, the amount of surfactant (typically 2-5% by mass) can impact reaction performance. Small amounts of an organic co-solvent are often needed to enable scaling of micellar conditions.[2][3] The identity and amount (typically 5-20% by volume) of co-solvent can impact reaction performance as well.
How it was applied to TAK-954: In developing the reductive amination to couple piperidine 16 to intermediate 6 in the second-generation process, it was found that co-solvent was necessary to stabilize the reaction mixture and prevent precipitation and gumming of reaction components and the product. A variety of co-solvents were screened and methanol was ultimately identified as the best-performing co-solvent.
Strategies to Develop Isolations from Aqueous Media
- Consider avoiding an intermediate isolation altogether with a telescoped sequence. Because the same reaction medium, namely water, is used in each synthetic step, intermediate isolation is not always necessary. Instead, a crude product mixture can sometimes be carried on to the next step without isolation. Telescoping one reaction into the next in this way can offer dramatic efficiency improvements, avoiding all of the materials and waste generated during work-up and isolation.
How it was applied to TAK-954: In the second-generation route, piperidine fragment 16 was prepared in a 3-step telescoped sequence – hydroxymethylpiperidine 12 was carbamoylated, the primary alcohol oxidized to the aldehyde, and the aldehyde converted to the bisulfite adduct without any isolations. This sequence was enabled by using water as a common medium across all three transformations. Although other telescoped sequences were explored in the second-generation route, none were implemented as the accumulation of salts and byproducts across synthetic steps was found to inhibit the downstream crystallization of products. - Control solubility with pH if relevant. When starting materials, intermediates, and products feature acidic or basic functional groups, their water solubility is often pH dependent. Increasing pH may lead to dissolution of acidic substrates, while decreasing pH may lead to crystallization of acidic products, and vice versa for basic substrates and products. Controlling the addition rate of an acid or base to a product mixture can lead to controlled crystallization of a product from aqueous media.
How it was applied to TAK-954: pH control of solubility was the primary strategy used both to achieve dissolution of reaction substrates and to crystallize and isolate intermediate products in the second-generation route. For example, the presence of the acid functional group in starting material 10 allowed for full dissolution of the material in water under basic conditions during the benzimidazole cyclization. After completion of the reaction, slow addition of HCl led to crystallization of benzimidazole 11 as the acid functional group was still present. A similar strategy was used to isolate intermediate 6 and crude TAK-954, both of which crystallize under basic conditions. - Be on the look-out for opportunities to implement reactive crystallizations. In cases where reaction substrates are water-soluble and the product has poor water solubility, a reactive crystallization where the product crystallizes as it forms can be developed. Reactive crystallizations are highly efficient as they avoid the need introduce additional materials, energy, or time to isolate a product.
How it was applied to TAK-954: In the second-generation process, a reactive crystallization of amide 6 was developed. Under the basic reaction conditions, the coupling partners, acid 11 and amine 4, are water-soluble, while amide product 6 has poor water solubility. Because the amidation reaction is rapid (complete in <10 min.), the amide product was observed to gum out of solution in an uncontrolled way as it formed. In order to reduce the degree of supersaturation of the amide product and encourage controlled crystallization, the rate of product formation was slowed by splitting the charge of the TCFH coupling reagent into three equal portions, waiting 15 min. between charges. Addition of THF co-solvent also helped to decrease the supersaturation of the product, allowing for a more controlled crystallization. - And finally, don’t forget about good process design principles. Traditional process design principles are just as relevant in aqueous conditions as they are in solvent-based processes. Replacing organic solvent with water is a strategy to improve process sustainability, but on its own it does not guarantee a sustainable process. We should also strive to minimize waste generation and select safe, low-impact starting materials, reagents, and catalysts.
- J.D. Bailey, E. Helbling, A. Mankar, M. Stirling, F. Hicks, D. K. Leahy, Green Chem., 2021, 23, 788−795.
- F. Gallou, P. Guo, M. Parmetier, J. Zhou, Org. Process Res. Dev. 2016, 20, 1388−1391.
- N.R. Lee, F. Gallou, B. H. Lipshutz, Org. Process Res. Dev. 2017, 21, 218−221.